Driving Sustainability In Engineering
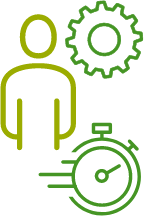
Energy consumption data monitoring
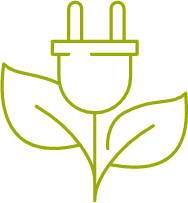
Energy efficient new plant & equipment
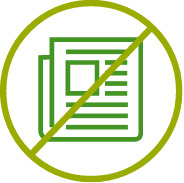
Paperless environment
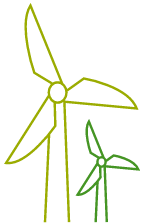
Renewable energy generation
Sustainability is not a destination. It is a continual path that takes us to new heights in quality. It delivers new approaches to how we work. It results in ever greater efficiency. And it provides new opportunities to innovate.
Within Middlesex Aerospace, our sustainable journey began long ago. From reducing waste, increasing recycling and changing our approach to energy usage, we are committed to minimising the impact of our business on the environment.
Minimal Waste
As raw materials are transformed into critical, highly precision-engineered components, by definition we create waste. Swarf, the material losses from machining, are aggressively recovered to ensure metals fragments so not enter the refuse chain. Compactors simplify the handling and removal of swarf, reducing collections and helping our recycling partners to operate more efficiently.
Recycling during manufacturing also includes the coolants and lubricants used within machining processes. By reclaiming these fluids, we ensure they do not enter water courses. Instead, they can be re-used, cutting down on the disposal of fluids. Similarly, tooling such as cutting heads which reaches end of life are not thrown away. Instead, they are sent for refurbishment or recycling into raw material for other manufacturing processes.
We take the same approach to even the most basic materials that arrive within our facilities. Paper and cardboard used in packaging is moved into the recycling chain. And wooden pallets and crates are collected by a partner for repurposing into furniture, DIY and craft projects.
Searching For Sustainability
Reducing our impact on the environment can be found in every aspect of our operations. Take for example is our commitment to improve efficiency in our capital equipment by investing in more efficient, automated machinery. This has lowered our energy consumption and allowed for continual 24/7 operation, removing energy wasted through time-consuming startup procedures.
Then there is the most visual aspect of energy consumption – lighting. Over 90% of the lighting throughout our facilities is by LED technology, significantly reducing the energy consumed within offices and production areas.
And our adoption of lean processes, integrated into the supply chain, we can drive efficiency and reducing waste. By digitising our design processes we reduce the need to create energy-intensive prototyping, as well as help reduce reactive maintenance.
But these are not definitive solutions. Just as sustainability has no end, so we never rest to find new ways to improve. And while our efforts to be a sustainable business stretch back over two decades, we continue to look ahead and search for better solutions that move us closer to Net Zero.
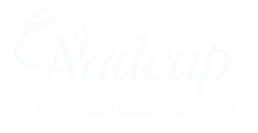
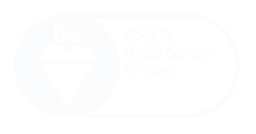
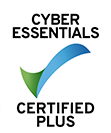
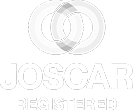